ピッキングミスゼロ達成!レーザーピッキング
12,054 views
部品取り出しミスによるロスを防止します
ピッキングは簡単そうで実はとても重要な作業です。正しくピッキングできないことが、やりなおしによるタイムロスや、後工程でのミス発覚によるライン停止原因にもつながってしまいます。
レーザーピッキングは必要な情報を自動で収集し、素早く探し出せる次世代のシステムです。集荷作業の三要素 ”置く” ”探す” ”取る” を容易に実現します。
大手自動車メーカー様にご採用いただき、導入後のピッキングミス0件を達成しております。
レーザーピッキング 5つのメリット
メリット | 概要 |
誤品不良ゼロ | 作業者の部品取り間違えに対し、音と振動でその過ちを伝えます。 |
作業効率化 作業者支援 |
作業者に対して効率の良い導線順にレーザーが指示を出して導きます。部品の位置を覚えていない初心者でも簡単に作業できます。 |
配線レス | 部品棚には配線や工事等の施工が一切必要ありません。 |
棚レイアウト変更 | ロケーション変更に際しても、短時間で容易に対処できます。 |
両手で作業ができる | ハンディリーダーを使わないので、両手で作業ができます。 |
システム概要
ピッキング部品情報をもとにピッキング指示と誤品判定をおこなうシステムです。ウェアラブル端末とレーザーポインタを使用しております。
ご利用シーンと導入事例
ご利用シーンとしては先入れ先出しの徹底、棚卸し作業の円滑化、取り間違い防止等が挙げられます。また、導入前は5~6件/月のピッキングミスが発生していたお客様も、本システムの導入後はミス0件となりました。
ハードウェア構成図(事例)
サイト内検索用ワード:IoT、自動化、ITソリューション
この記事を書いた人
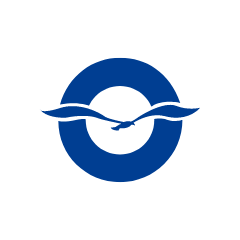
NADEX Magazine編集部
モノづくりに関わる皆様へ、取り扱いメーカー情報はもとより、電子部品・電気部品・制御機器・設備機械などに関わるノウハウや情報をお届けいたします。
Tags: